Today, in Russian villages, horses are still kept on private farms. And a horse, in order to use it effectively, needs a cart and a sleigh. Of course, there are enterprises that produce summer and winter carts. But there are few of them, and the price is not always high for the peasant.
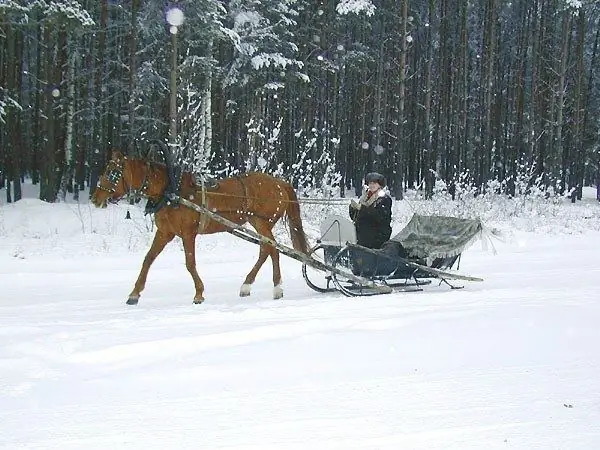
Necessary
iron pipes, metal corner, birch bars and round timber, grinder ("grinder"), electric welding and welder skills
Instructions
Step 1
Of the two types of carts, in order to save some funds of the peasant budget, it is easier to make a sleigh with your own hands. The most time consuming part of a sled is the runners. The manufacture of wooden runners presupposes a certain technology, provides for the sufficient qualifications of the master. But the runners can be made of metal, from pipes, and it is much easier.
Step 2
Pick up two pipes with a diameter of 50-60 mm and a length of 3.5 m.
At a distance of about 2.5 m, start bending one, then the second pipe into arcs, using any point of support for this. It is desirable that this be a kind of eyelet through which the pipe can be gradually pushed, ensuring a uniform bend.
Bend also a few and the rear end of the runners to make it easier for the sled to move in reverse.
Achieve, as far as possible, an exact match of the outer diameters of the arcs with a value of 740-750 mm. This will be the highest height of your sleigh.
Step 3
Now you need to weld the deck frame. In practice, corners from old armored beds are used for these purposes. Leave the lengths of the bed frames as they are. They will be within 2 meters, as little as possible. Use the grinder to free them from unnecessary segments.
Step 4
Measure 4 more lengths of the corner of 60 cm and also cut off with a "grinder". Weld two of them to long 2-meter workpieces, forming a regular quadrangle. Another one in the middle for durability. Weld the third section to the upper ends of the runner pipes, joining them together - this will be the highest place in the sled.
Step 5
Prepare kopyla (or filly, in the people) 10 cm long from the remains of pipes. They will need 6 pieces on each side, for a total of 12. Weld all the hoops to the frame at the ends and proportionally along the length.
Step 6
Now install the frame of the future flooring almost flush with the arches and weld the filly to the runners. To attach the shafts to the runners and the deck frame, weld on each side a plate with a thickness of at least 8 mm and dimensions of about 10x15 cm. They must have burnt or drilled holes of a suitable diameter for the hooks.
Step 7
You now have a sled frame. Do the rest with wood.
Pick up or prepare a good beam 1400x100x60 (you can use the appropriate round timber, preferably birch), on the back cross member of the side bends. Fasten the timber with bolts of the appropriate size to the rear corner of the deck frame, after having drilled holes in the timber and in the corner of the frame.
Step 8
Also fasten the front bar on the bolts at the corner holding the ends of the runner arcs. Its ends should protrude at least 10 cm beyond the edges. Prepare a couple of two-meter round birch logs, at least 5 cm in diameter, and connect the edges of the front and rear crossbars with them.
In the figures: 1 - runner, 2 - undercut, 3 - forged bracket, 4 - hoop, 5 - bolts for fastening undercuts, 6 - strip, 7 - frame, 8 - side branches, 9 - flooring, 10 - shield, 11 - front bar, 12 - steel bar, 13 - rolling pin, 14 - cross member of side branches, 15 - rope, 16 - transverse boards of the shield.
Step 9
Line the deck frame with planks and secure.
Install the front transom bulkhead at a slight incline by attaching it to the front cross-member and to the deck-mounted timber.
Make boards to your taste - either corded or solid, for example, from tin.
Harness your horse. Lay the fragrant hay and go!