In the course of the activity of any enterprise, regardless of its form of ownership and manufactured products, managers of any level constantly have to make management decisions. Methods of mathematical and statistical modeling are used to calculate, analyze and choose the best solution from all existing solutions.
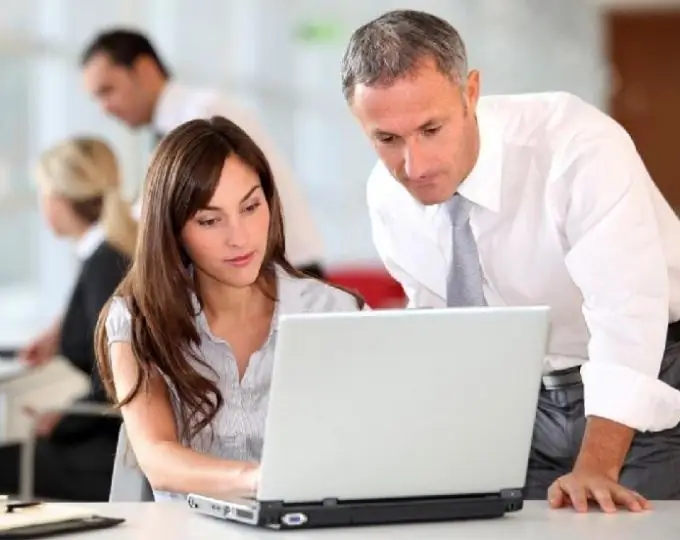
Instructions
Step 1
The advantages of the modeling method include lower cost compared to experimental options in reality. Without wasting time on such experiments, modeling the options for the development of the situation, the manager can significantly reduce the time for choosing the right solution that meets the optimization parameters set for each specific case - one or several. Using various algorithms, it is possible to simulate various scenarios for the development of events and fairly accurately evaluate the results obtained in a particular case, as well as those conditions that will optimize them.
Step 2
The disadvantages of modeling methods include the simplification of the processes that occur in reality. Some models, which are as close to real conditions as possible, may be too complex and may take more time to develop than experiments that can be implemented directly in life. In models, it is difficult to account for the influence of factors that cannot be calculated. But in most standard cases, typical for the main part of production processes, simulation is the most effective way to make the right decision.
Step 3
The creation of a model, which can be physical, analogous or mathematical, of course, somewhat simplifies the process, since none of the models can accurately simulate a real process, which is influenced by many random factors. But taking them into account allows us to make the model as close to reality as possible and, therefore, as reliable as possible, which will allow us to make the most correct managerial decision for a given situation. Simplification, which is inevitable in the process of modeling, should not have a significant impact on this reliability and violate the existing in reality patterns of functioning of the modeled system.
Step 4
In manufacturing, many activities are carried out by building models. Modeling is used to make decisions on economic, financial, social and technical development; organization of production processes; marketing; material incentives for employees; staffing; accounting and general management issues. The use of computer technology makes it possible in the shortest possible time to get all the options for the development of the situation using simulation, network, algebraic and statistical models, as well as models of linear programming, stocks and queuing theory.