Aluminum has ceased to be considered the rarest material and has firmly entered our life, becoming a necessity. Applications for aluminum continue to expand. We owe the creation of light, but, despite this, durable structures to this material. When starting to weld aluminum, the welder needs to get acquainted with its features and welding technology.
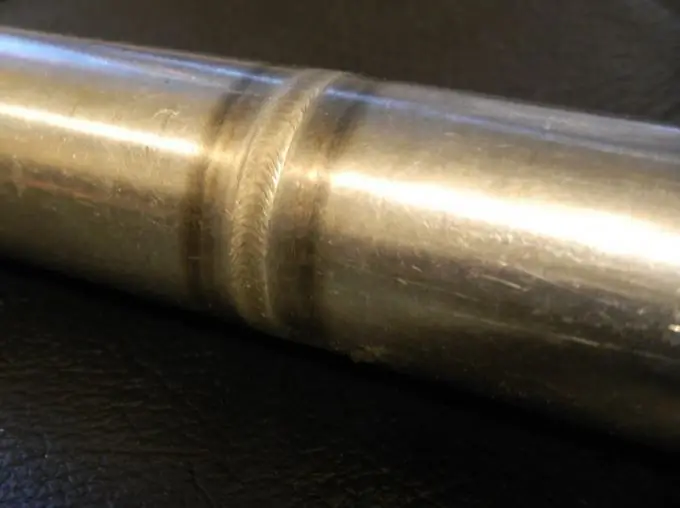
Necessary
- - welding machine;
- - gas cylinder;
- - burner;
- - flux;
- - electrodes;
- - solvent;
- - water;
- - liquid glass;
- - trisodium phosphate;
- - soda ash.
Instructions
Step 1
Prepare parts for welding. Profile edges and remove oxides. Degrease and remove surface contamination using organic solvents. White spirit, solvent RS-1, RS-2 or technical acetone are suitable. You can also treat the surface in an alkaline bath. To do this, prepare a solution where 1 liter of water has 30 g of liquid glass and 50 g of technical trisodium phosphate and soda ash.
Step 2
Process the surface for 5 minutes at 70 ° C. Thus, the old oxide film containing adsorbed moisture will be removed from the parts. The oxide film can also be removed by scraping, after which the edge must be degreased again with a solvent. After stripping, the parts can be stored for 2-3 hours before welding.
Step 3
Before contact seam and spot welding, additionally clean the overlapping surfaces with metal rotating brushes. If the thickness of the sheets to be joined is higher than 0.3 cm, remove the clad layer by deep etching, which will prevent the formation of lack of fusion. Carry out the etching in a bath of an aqueous solution of sodium hydroxide (50 g per liter of water) at a temperature of 70 ° C for 1-2 minutes. Cut the ends of the parts, for example, on a metal-cutting machine.
Step 4
When welding aluminum alloys by fusion, it is advisable to perform butt joints. To eliminate oxide inclusions in the seams, use washers with a groove into which they will be removed. In argon-arc welding, oxide inclusions will be reduced by applying fluxes to the ends. Overlap joints are made by seam and spot resistance welding. The ratio of the thickness of the parts to be welded should not exceed 1: 2. Butt joints are used for flash butt welding.
Step 5
For gas welding, it is recommended to use a flame of an O2: C22 mixture. AF-4A flux is preliminarily applied in the form of a paste or is introduced with a filler rod during welding. For the filler metal, an aluminum welding wire is used, the diameter of which depends on the thickness of the metal.
Step 6
Gas-shielded arc welding is widely used to join aluminum. Argon or a mixture of argon and helium is used as a gas. Argon purity must be at least 99.9%. If welding is carried out with a consumable electrode, you can use argon with the addition of O2, but not more than 5%.
Step 7
Manual electric arc welding is carried out with a coated metal or carbon electrode. Carbon arc welding should be done with direct current of direct polarity. In arc welding with metal electrodes, a solution of dextrin or sodium chloride in water serves as a binder. The process takes place on a direct current of reverse polarity.
Step 8
If the thickness of the butt joints is more than 0.4 cm, automatic arc welding is used with a layer of flux. It is produced by a consumable electrode. The power supply requires a direct current of reverse polarity. The flux should be with reduced electrical conductivity, for example, ceramic. It is mixed with an aqueous solution of carboxymethylcellulose, rubbed through a sieve and calcined for 6 hours at a temperature of 280-320 ° C. Welding is carried out with a split electrode.