Copper, like other non-ferrous metals and alloys based on them, is difficult to weld. Difficulties in welding are due to the high thermal conductivity of copper, as well as its tendency to oxidation and strong absorption of hydrogen in the molten state. All of the above features must be taken into account when carrying out welding work. One of the most common methods for welding copper is manual carbon arc welding.
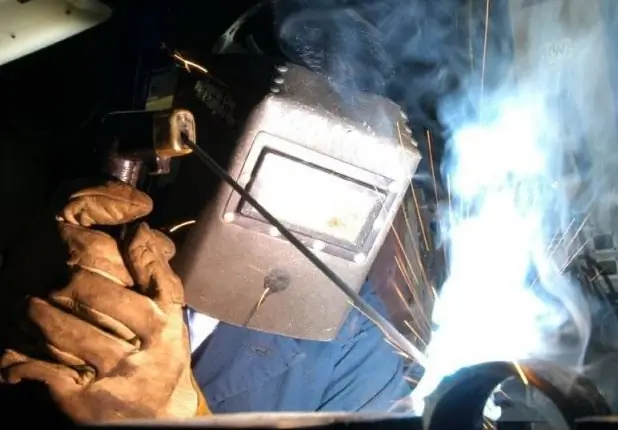
Instructions
Step 1
Prepare the parts to be welded. It should be noted that this welding method is advisable to use only for low-critical products and with a copper thickness of less than 15 mm. Clean the edges of the parts and the adjacent surface. Welding is carried out using cone-sharpened electrodes, with direct current of direct polarity. Place the electrode at an angle of 75-90 degrees to the workpiece to be welded. When using a carbon electrode, welding must be carried out with a long arc. The recommended current density at the electrode is 200-400A / cm2.
Step 2
Use M1 red copper rods as filler material. When using manual welding using a carbon electrode, the filler material should not be immersed in the bath. Hold the additive at an angle of approximately 30 degrees to the workpiece, 5 mm from the surface of the molten layer.
Step 3
Welding is carried out under fluxes from borax or a mixture of borax with magnesium, boric acid or other components. The use of filler material and flux reliably protects the molten material from oxidation. The flux should be applied to the edges to be welded or the surface of the bar, previously moistened with water glass, and then dried in air.
Step 4
It should be noted that if the thickness of the product is 5 mm, the cut angle at the edges of the butt joint should be up to 90 degrees. Use a graphite base for welding. Weld the butt seams in one layer on one side. This will help to avoid deterioration in mechanical properties.
Step 5
Post weld forging along the entire length of the seam. If the metal thickness is less than 5 mm, forging can be carried out in a cold state. With a metal thickness of more than 5 mm, post-welding forging should be carried out with the product heated to a temperature of 600 degrees, followed by rapid cooling. Clean the joint with a nitric or sulfuric acid solution and rinse with water to remove any remaining flux.