Now you can order or buy magnets of any size from the required material. Finding the right size, factory-made magnet is the best option. However, if this is not possible, you can try to saw the usual ferrite.
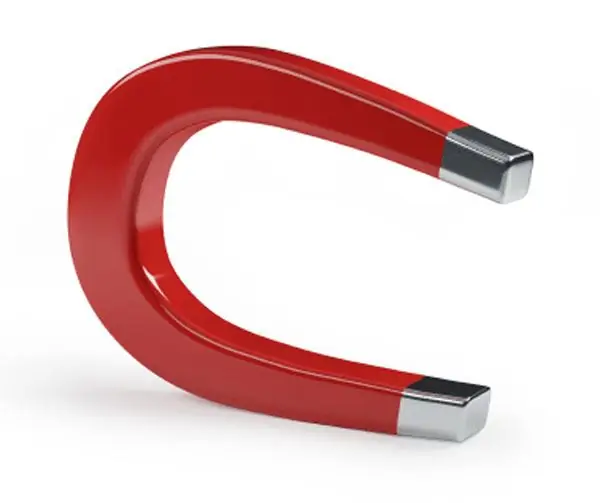
It is necessary
- - Vise;
- - sharp cutting tools for hard surfaces (for example, diamond thread or diamond-coated cutting disc for power tools);
- - water for cooling.
Instructions
Step 1
Not every magnet can be sawed. For example, powder magnets fall apart during machining. But ferrites (if they are not overheated during sawing) do not lose their properties and are quite technological. However, even a small magnet should be tested for hardness. Try to make a small cut before starting work.
Step 2
Select a tool for processing. The "grinder" (electric angle grinder) is best suited for this purpose. Choosing a cutting part for it, stop your choice on a diamond disc for a stone. If you only have a hacksaw for metal, take a diamond-coated blade for it, a diamond thread. Do not use an ordinary sheet for metal in any case. You should also not try to saw large magnets with a hand tool - this is a very time-consuming process.
Step 3
Draw a cutting line with a simple pencil. It is also advisable to outline this line with a sharp object (for example, a nail). Clamp the magnet securely in a vise.
Step 4
Any ferromagnet has a so-called Curie point (or temperature). An overheated magnet loses its properties. Therefore, regardless of which processing method you choose, take care of cooling the magnet surface during processing. To do this, stock up on enough water.
Step 5
Now you can start sawing the magnet. During work, make sure that the cut is even on all sides. This will allow you to get a neat cut and also reduce overheating problems in certain areas.