In modern individual construction, new technologies are widely used, but sometimes there is a need for simpler things. What if, say, you need a tin pipe of a certain size? Such designs are often used for the manufacture of water drainage systems. If it was not possible to find a pipe of a suitable size in the retail network, you can make it yourself.
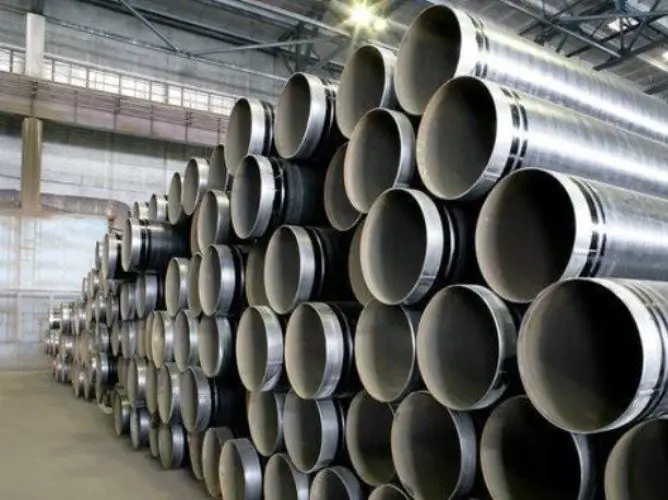
It is necessary
- - thin sheet metal;
- - scissors for metal;
- - metal bar;
- - steel or aluminum rivets;
- - crafting table;
- - roulette;
- - ruler;
- - metal scribe;
- - an ordinary hammer;
- - a wooden hammer (mallet);
- - mandrel;
- - pliers.
Instructions
Step 1
Select the material for making the pipe. You will need a sheet of thin galvanized sheet metal. Such metal does not corrode and is relatively easy to process with the most common tools.
Step 2
Draw a sketch of the future pipe. Place the dimensions on a piece of paper. Then transfer the pattern to a pre-prepared sheet of tin. When making a pattern, keep in mind that the width of your workpiece should be equal to the diameter of the future pipe, to which you should add about one and a half centimeters. For a straight pipe, the length of the workpiece should be slightly larger than the required size.
Step 3
Using scissors for cutting metal, cut the drawn pipe blank from the sheet. Place it on the edge of a workbench or other flat, horizontal surface. Along the entire length of the sheet of tin, draw a fold fold line on one side, stepping back from the edge of half a centimeter.
Step 4
Now align the line you drew with the edge of the workbench. Bend the edge of the sheet down with blows with a mallet. Now turn the workpiece over and bend the edge to the sheet with very light blows of a wooden mallet.
Step 5
Turn the sheet of metal over again and use a mallet to bend the edge a centimeter, but in the other direction. The bend profile should resemble the letter "G". Place the workpiece prepared in this way in a mandrel and gently bend the edges of the sheet towards each other with your hands.
Step 6
Connect the edges of the sheet in a "lock" so that the smaller of the edges is caught on the one that has a larger size. Use pliers to seal the edges, then use a metal strip and a regular hammer to tap the joint well.
Step 7
To give the finished pipe extra strength, fasten the edges of the tin pipe with aluminum or steel rivets. To do this, prepare holes in the pipe, taking a step between them about three centimeters. Insert rivets of a suitable size into these holes and make the connection using a regular hammer. The pipe is now fully operational.