Not all metals have the same casting properties, and some cannot be cast at all. Casting properties depend on the structure and chemical composition of the metal. Easily cast metals with a low melting point; steel has the highest melting point. All metals are subdivided into non-ferrous and ferrous. Iron and steel are ferrous, and all non-ferrous metals are nonferrous.
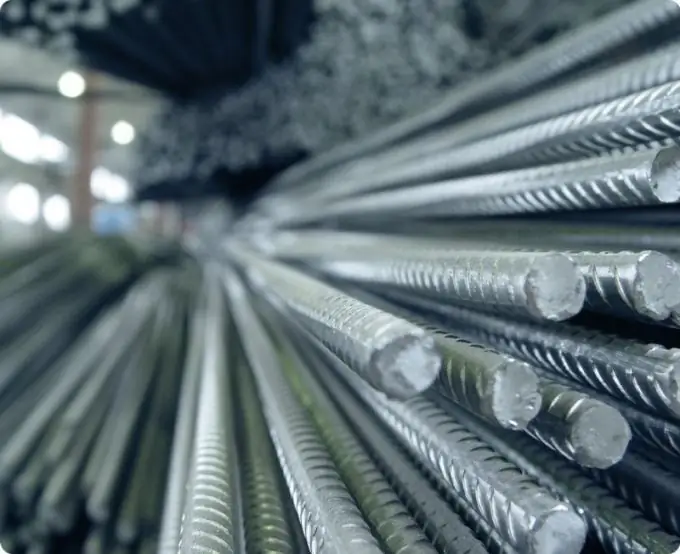
Instructions
Step 1
The main casting methods include: centrifugal casting, static casting, injection molding, and vacuum casting.
Step 2
For metal pressure casting, a steel mold is used, which can be multi-cavity. The advantages of this method are high surface quality, high productivity and accurate product dimensions, as a result of which the need for machining is minimized. Zinc, aluminum, tin and copper are suitable for die casting and melt at a low temperature. Casting machines can be of 2 types: with a hot chamber and cold.
Step 3
To melt the metal, immerse it in a hot chamber, and under the action of a piston and compressed air pressure, the liquid metal will be squeezed out of the hot chamber into the mold. A cold chamber casting machine is also used, but for lower melting metals.
Step 4
For centrifugal casting, pour molten metal into a sand or metal mold that rotates on its axis. The metal is thrown to the periphery of the center sprue under the action of centrifugal forces. All cavities are filled, the metal hardens and forms a casting.
Step 5
Static casting is used most often for metal, glass and plastics. To do this, melt the metal and pour it into the cavity of the stationary mold until it is completely filled. Soak until hardened.
Step 6
Alloy steel and titanium vacuum melt. After the metal has melted, pour it into multiple waves placed in a vacuum, this method helps to reduce the gas content of the metal. Vacuum castings can weigh several hundred kilograms. If there is a need for a casting weighing about 100 tons, then pour the metal into a vacuum chamber with installed casting ladles. Large vacuum chambers are pumped out by special systems with multiple pumps.
Step 7
The most accurate casts are produced using disposable models. Previously, disposable molds were used in sand casting, but now foam molds are increasingly being used. For single-use or large castings, cut out the foam model with a heated nichrome wire according to a template, or on a milling machine. The casting obtained by such a model will have a competitive presentation and high accuracy.