It is already quite difficult to imagine life without a mirror, this object is so convenient and necessary. Over the centuries, the manufacture of mirrors has turned from an almost magical act into an ordinary procedure.
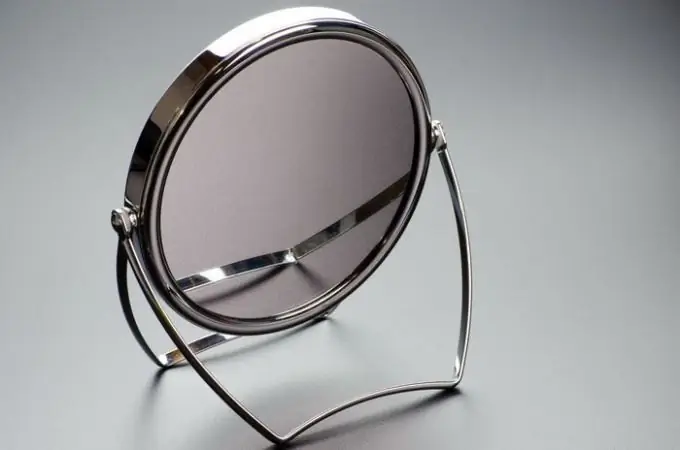
In the modern production of conventional mirrors, harmful mercury has not been used for a long time, which caused a lot of trouble for mirror craftsmen. Nowadays, aluminum or silver is used instead of mercury. The minimum set for making a mirror is a smooth sheet of glass, a suitable abrasive for grinding, demineralized water, degreasing agents, a solution of silver salts, tin, chemicals for the reconditioning process, and paint for the protective layer.
Since ancient times, reflection has been endowed with magical properties.
Mirror production technology
The glass sheet is transported by a conveyor to the grinding and washing area. Cerium oxide (an unstable metal made from lanthanides) is used as an abrasive for grinding. Both sides of the glass sheet are brought to absolute smoothness, then washed with heated distilled water, which dissolves fatty contaminants.
Distilled water is good because it doesn't leave any marks on the glass. A perfectly clean surface is needed to create a reflective layer without any problems. The fact is that the interaction of reagents with minerals that can remain on the glass when using ordinary water can lead to defects in the mirror coating.
After that, the glass is prepared for silvering. Silver cannot fix on the glass surface, so a thin layer of liquid tin is sprayed onto a polished sheet of glass. Further, when the necessary reagents are added, the solution of silver salts reacts with this tin layer.
Initially, mercury took part in the process of making mirrors, which significantly reduced the life of the craftsmen. The production of one mirror took an average of twenty days.
A thin film forms on the glass sheet, which is the reflective surface. It is soft, unstable, therefore a dense protective layer is required. Sheets checked for coating defects are allowed to the next stage.
The final stage of making mirrors
Soft silver film, which is, in fact, a mirror, requires good protection. Short-lived mirrors have a thick layer of protective paint on the back surface. For durability, a thin layer of copper is sprayed onto the finished product and paint is already applied to it. Drying of paint and copper is carried out in several stages at different temperatures. After complete drying, the mirrors are tested for defects again, if at this stage fragments with bubbles or dark dots are found, they are cut off.