With the use of new technologies in construction, the need for the use of tin pipes is gradually disappearing. Today they are used more as decorative elements. Tin is a thin sheet steel, subject to corrosion, therefore, galvanized roofing iron is used to make weather vane, beautiful drainpipes, visors over them, covers over chimneys or filigree laces.
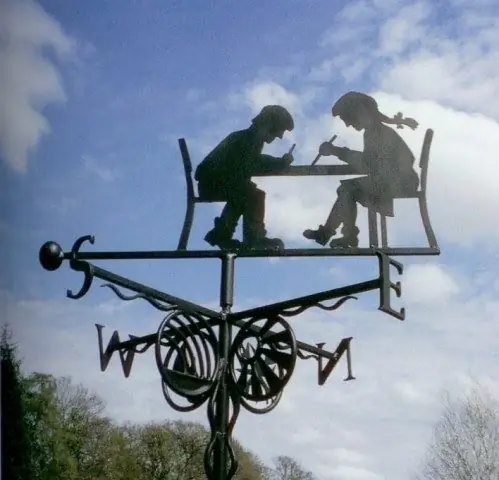
It is necessary
iron sheet 0, 5-0, 7 mm thick, a wooden hammer, scissors for metal, a metal bar
Instructions
Step 1
Thin tin is a favorite material for homemade smokehouses and saunas. Tin pipes are also used as samovar. They increase traction and remove smoke. Making a tin pipe is not difficult. You need a sheet of thin roofing galvanized iron with a thickness of 0.5-0.7 mm, a wooden hammer - a mallet, metal scissors, a metal bar, an ordinary hammer and pliers. The iron sheet should be even, smooth, with right angles.
Step 2
Draw an expanded pipe pattern on a sheet of iron. This can be done with chalk or some sharp object. The width of the workpiece should be equal to the diameter of the pipe + 1.5 cm, the length - to the length of its straight section. Cut the drawn workpiece with scissors for metal.
Step 3
Put the workpiece on the edge of the workbench and draw on one side (along the length) of the sheet a flange bend line - 0.5 cm. Align the drawn line with the edge of the corner on the workbench and bend the edge down with a mallet. Turn the sheet over and use a mallet to bend the edge to the sheet.
Step 4
Turn the workpiece over and bend the edge 1 cm wide on the other long side, but on the other side. Then fold this edge again, i.e. in profile, the bend will have the shape of the letter G.
Step 5
Insert the workpiece into a mandrel (a pipe sector of the required diameter, however, some can do without it), carefully bend the edges of the pipe towards each other. Join the edges into a lock so that the smaller edge catches on the larger one. Seal the lip with pliers. Using an iron bar and a hammer, lay the edge on the sheet, tap it well.
Step 6
You can also fasten the ends of the pipe using aluminum or steel rivets. Then the edges are bent at an angle of 900 towards each other. Holes for riveting are pre-drilled in them at a distance of 3 cm. The blank sheet is bent in the opposite direction so that the edges coincide and are on the outside of the pipe. Then the edges are fastened with rivets. In this case, an external seam is obtained, which is not very convenient to use.