Self-repair of an electric drill is available to everyone who is at least a little familiar with electrical engineering and has a basic set of tools. Since most power tool models are similar in design, the repair process will be similar.
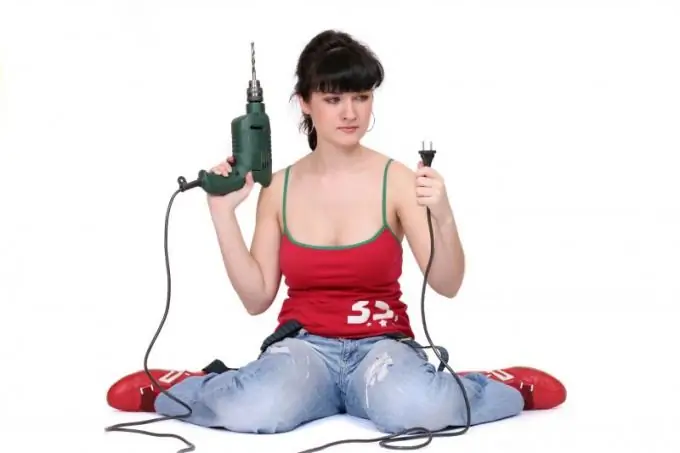
Necessary
- - set of tools;
- - multimeter (tester);
- - sandpaper and lapping paste
Instructions
Step 1
Disassemble the drill. To do this, remove the holder and loosen the clamp by unscrewing the handle counterclockwise. Then remove the mounting screws around the perimeter of the case. Use a screwdriver to pry the halves of the case and carefully separate them.
Step 2
Pull back the brush spring and release it. To remove the motor armature, pull out the brush halfway or all the way out, depending on the design. When installing them, make sure to maintain the original position of the brushes. Their wear can be determined by whether the spring touches the brush holder. Replace worn parts with new ones.
Step 3
If it is not possible to get new brushes, make them yourself from the brushes of any household commutator motor. The original brush must meet the following requirements: the size must not be less than the required one, the contact terminal must be intact and of sufficient length for the new installation site. It is better to choose the type of brush carbon-graphite, although this does not matter for emergency repairs.
Step 4
Raising the stator of the electric motor, remove the cartridge with the bearing and the gear wheel, and then the rest of the gearbox parts together with the armature and the second bearing. Breakdowns of the gearbox, gears and worm gear are rare and are associated either with damage to the electric drill housing or its distortions.
Step 5
The wear of the rotary hammer bearings cannot be determined by ear during operation. Therefore, periodically check them together with the motor brushes. Determine a visually worn bearing by the clearance. To do this, while holding the bearing shaft, try to wiggle the outer race towards the direction of the shaft. A gap of 2 mm or more indicates critical wear.
Step 6
Assess the condition of the motor armature. Slight darkening of the surface is normal. The presence of grooves and burnouts can indicate permissible overloads during operation. If the armature looks normal, check the windings for open or short circuits. Measure the active resistance of the windings at their terminals. If it is less than 4 ohms on each, and when the drill is turned on, the bed begins to heat up, the cause of the malfunction is an inter-turn circuit. To eliminate this problem, rewind the winding.
Step 7
To detect the short circuit of the armature winding, connect one terminal of the multimeter to the plate, and gradually pass the other along each winding, starting from one edge to the opposite in diameter. The values of normal resistances for each model of the electric drill are different. Check with the user manual or the service center. An abnormally high resistance on the armature plates means that the windings are broken.
Step 8
To grind scratches and grooves on the engine manifold, clamp the free end of the shaft into the chuck of another drill and at medium speed grind the manifold with fine abrasive glass sandpaper, pressing it evenly over the entire working surface. After sanding, sand with lapping paste. Turn large furrows and burnt areas on a lathe.