Steel is one of the most demanded materials today. It consists of an alloy of iron with carbon, sometimes additional elements are added to give the desired properties to the material. The metal is produced using a complex technology in special furnaces. Steel production is a difficult technological process.
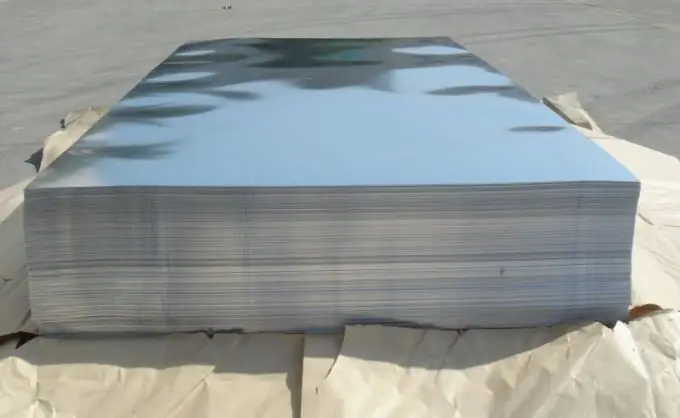
Instructions
Step 1
Steel production begins with ore mining. Iron ore is a natural iron oxide, i.e. iron in conjunction with oxygen. To obtain iron, it is necessary to purify it from oxygen and rock by melting. For this, iron ore is immersed in a special furnace, where it is processed under a stream of hot air. The temperature in such a furnace reaches 2000 ° C.
Step 2
The resulting iron is delivered to the blast furnace using special cars designed to transport the molten ore. To obtain steel, lime and oxygen are first added. Lime is used to remove unnecessary impurities from the material - slag. Depending on the type of metal, coke and dolomite, a special mineral composed of calcium and magnesium salts, can also be added.
Step 3
Then the mixture turns into liquid iron at a temperature of about 2000 ° C. The molten cast iron is sent to a special conveyor workshop. The quality of the obtained metal is determined by casting samples.
Step 4
In the next stage, steel production begins in the steelmaking shop. Impurities are added to cast iron - scrap metal, which helps to control the melting point and impart appropriate properties to the material. Other metals are most commonly used, such as aluminum. Cooking is carried out at a temperature of 1300-1700 ° C and water is used to protect against overheating.
Step 5
Finished steel is delivered to the casting department, where billets are poured by special boilers. Then the blanks fall into the rolling mill and are rolled onto sheets using special shafts. After that, the steel is galvanized in a bath with molten zinc and sent for shipment, from where it is delivered to other industries to obtain the final product - steel products.