The welded track is widely used on modern railways. Elimination of joints allowed to reduce energy and fuel consumption, reduce wheel wear and resistance to train movement.
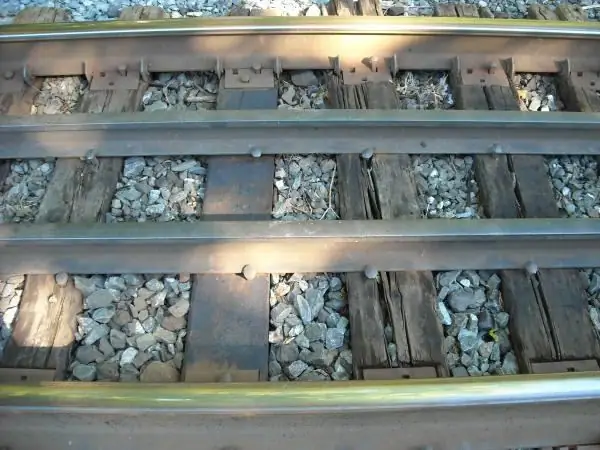
Advantages of a seamless path
The dynamic impact on the track is weakened by the elimination of joints. In addition, the organization of a continuous welded track allows you to significantly save metal - up to 1.8 tons per kilometer of track. In turn, this reduces the cost of repairing and maintaining the railway.
If we talk about continuous welded rails, then their service life increases by about 20%. The service life of wooden sleepers is increased by 8-13%. A decrease in labor costs for the current maintenance of the track was recorded - by 10-30%.
Rail lashes for continuous welded track are made of thermally hardened rails that do not have bolt holes. These are P65 or P75 standard lengths. For welding, mobile or stationary contact welding machines are used. The welding process is carried out by an electrocontact method.
Before the summer and winter periods, it is necessary to adjust the length of the lashes. For this purpose, from two to four pairs of equalizing rails having a length of 12.5 m, or rails of variable length, are laid between the welded strings. A set of leveling rails laid on the track is called a leveling span.
To ensure high strength of the track, all rail joints in the equalizing spans are connected with six-hole plates and butt bolts, which are made of high strength steel.
Features of a continuous welded track
The jointless path began to be laid for a long time. At first, the length of the welded strings did not exceed 800 m. The strings were delivered to the haul by trains consisting of platforms equipped with rollers.
Long-term experiments were carried out. Since 1986, it has been allowed to lay lashes of a certain length. It coincides with the length of the block section and the haul. A number of requirements were established for the manufacture and operation of lashes.
The welded track has some peculiarities. The main one is that the length of the rail strings cannot change with a decrease or increase in temperature. When the temperature fluctuates in the lashes, compressive or longitudinal tensile forces arise.
In summer, in hot weather, this can cause the path to be thrown to the side. In winter, a gap may form as a result of a break in the lash.
In summer, in hot weather, this can cause the path to be thrown to the side. In winter, a gap may form as a result of a break in the lash. To avoid this, the continuous path is laid as follows. Crushed stone ballast and reinforced concrete sleepers with separate fastening are used.
A welded track is used on sections of high-speed traffic. In these areas, special attention is paid to the prevention of wave-like wear on the surface of the rails.