Japanese swords are considered the pinnacle of the development of medieval metallurgy and real works of art. The technology of their manufacture was kept secret by blacksmiths for a long time, and some subtleties are still unknown.
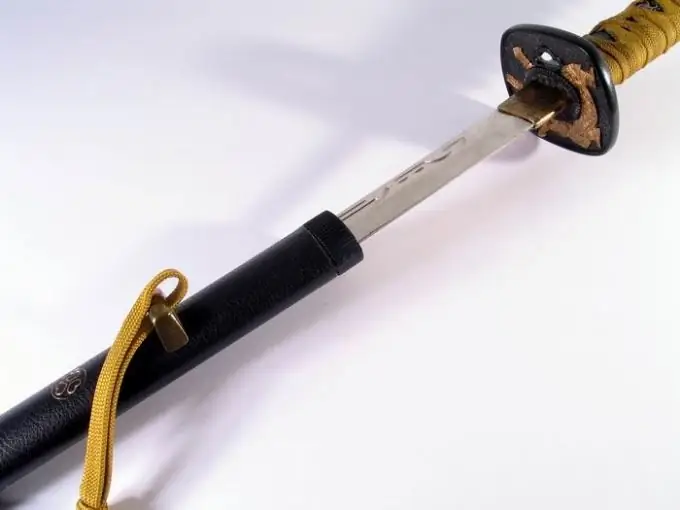
Smelt steel
Japan is poor in iron-containing ores, therefore, to obtain high-quality iron, billets were buried in the ground for several years or immersed in a swamp. During this time, harmful impurities and slags were removed from the iron. After the blanks were "matured", the blacksmith proceeded to forging. Iron ingots were transformed into plates, which were folded in half several times, reaching not only a multilayer structure of steel, but also an equal content of carbon in it along the entire length, which protected the blade from destruction due to the inhomogeneous composition.
Modern researchers believe that Japanese swords were only slightly superior to European counterparts, since the main technological stages coincided.
For the manufacture of a real Japanese sword, at least two types of steel were used: solid - with a high carbon content and ductile - low carbon. Blacksmiths combined steel of different hardness in order to combine the strength in the blade, necessary for the cutting edge, and flexibility, which protected the sword from damage when struck. The most complex swords used up to seven types of steel, but the resulting blades had the best characteristics.
After the formation of the blade blank, the stage of heat treatment began, that is, hardening. It is hardening that provides the cutting part of the sword with the necessary strength and resistance to mechanical stress. At the same time, the blacksmiths solved the problem of simultaneously maintaining the flexibility of the blade. This was achieved using the so-called uneven hardening technology. A special composition based on clay and ash with the addition of secret ingredients was applied to the blade, and the thickness of the layer was different: the thinnest was on the cutting part, the thickest was in the middle of the blade.
From the workpiece to the blade
The sword prepared in this way was heated to a temperature of approximately 760 ° C, after which it was sharply cooled. As a result, the metal changed its structure, reaching the highest strength in the area where the composition layer was the thinnest. In addition, a special pattern was formed on the border of the cutting part and the main surface, according to which the craftsmen evaluated the quality of the blacksmith's work. By the way, the curved shape of the blades in some cases was achieved precisely by deformation during the hardening process.
There are a lot of different myths heaped up around Japanese swords. The miraculous properties of samurai weapons are often promoted in Western films.
The final stages of creating a Japanese sword are polishing and assembly. To give the blade a shine, the master polisher used up to sixteen types of grinding stones of varying degrees of grain. After grinding, a patterned round guard and a handle, covered with the skin of a shark or stingray, were attached to the blade, which allowed the sword to not slide in the palm. The scabbard for the sword was made of varnished wood, in particular magnolia.