Worn tires are the largest-tonnage products of polymer-containing waste that are not subject to natural decomposition. This becomes the reason for the continuous accumulation of old worn-out tires. Therefore, the recycling and reuse of obsolete tires are of critical economic and environmental importance. At the same time, only about 20% of their total number is processed.
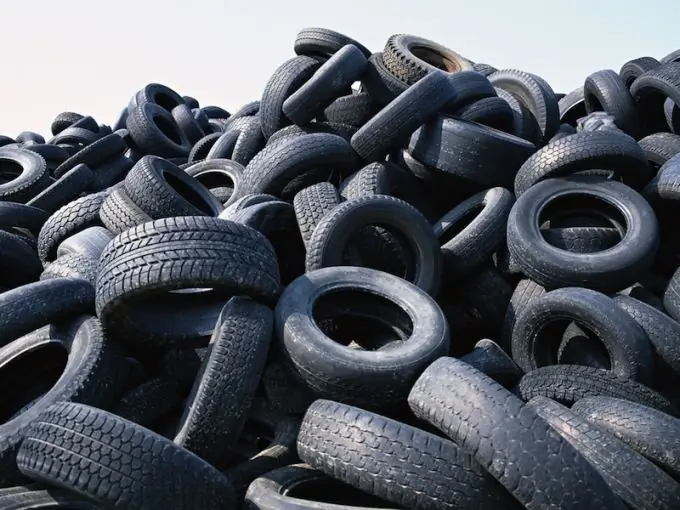
Instructions
Step 1
Worn tires are a valuable polymer material. 1 ton of tires contains about 700 kg of rubber, which, as a recyclable material, can be used for the production of technical rubber products, fuel, building materials and other products. Since the problem of recycling tires is very acute, recyclers of car tires are very often asked to accept used material for recycling.
Step 2
Tire recycling line. First of all, you should pay attention to the benefits of this production. Available raw materials for processing are obtained at a very low price, sometimes completely free of charge. The equipment itself works using frictional force without using chemical reactions. Its design is quite simple, wear-resistant, requires a minimum of maintenance, and has compact dimensions (occupies an area of about 200 m² excluding storage facilities). The production is environmentally friendly, since the equipment operates only on mechanical processes and emits exclusively recyclable materials - crumbs, textiles and iron. Chemistry, gases and noises are absent. This installation contains all the necessary equipment for the production of the final product - crumb rubber. The line for processing pays for itself in half a year - a year and requires a small number of personnel (from 2 to 5 workers without special qualifications).
Step 3
Description of the work of the mini-plant. This line processes worn-out tires into rubber crumb of different fractions: 5 - 40 mesh (up to 0.42 mm). By installing thin sieves, you can get crumbs of a finer fraction (up to 0.1 mm), but the line performance will drop. To obtain finer crumbs, you need to install deterators on the equipment. Also, during the production process, textile cord in the form of cotton wool and high-alloy crushed steel are removed from the tires, which can also be used or sold as recyclable materials.
Step 4
The capacity of the tire recycling line: 200 - 1000 kg of crumb per hour, depending on the raw material, the original size of the crumb and the model of equipment. That is, from 1, 2 to 1.5 thousand tons per year (300 days, 22 hours a day). The chip fraction can be adjusted by changing sieves (no more than two sizes at the same time). Also, for a 10-hour shift, the output of textile cord is up to 1000 kg, and metal cord - up to 200 kg (depending on the raw material).
Step 5
Characteristics of rubber crumb: the purity of the crumb for the rubber content of 99.8%; metal content less than 0.1%; the content of textile fiber reaches 0.2%; has a high purity of separation by fractions; the effect of thermal oxidation is completely absent; the color of the shavings is black.