Copper and aluminum wires can be connected by twist, threaded connection, terminal block and permanent connection. Each of these methods has its own indications for use.
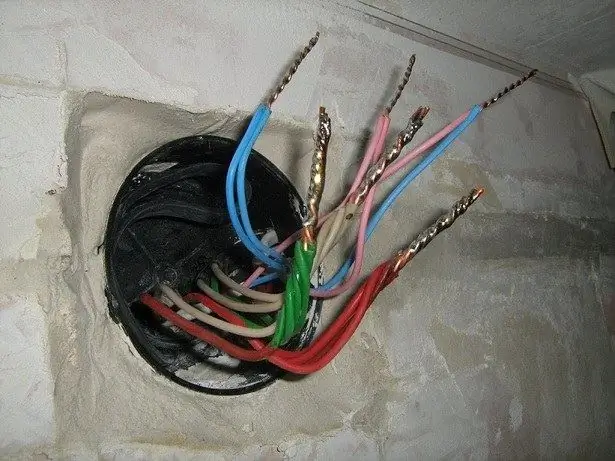
Necessary
copper wire, aluminum wire, screw, washer, terminal block, riveter
Instructions
Step 1
Twisting is the most common way of connecting wires from these materials, used when laying electrical wiring. However, it also has the lowest reliability. If twisted incorrectly, after a few years the wires will oxidize and the contact between the conductors will be broken. This can be avoided if the twist is done so that the conductors wrap around each other, eliminating the entanglement of one another.
Step 2
After the conductors are twisted, they must be coated with a waterproof protective varnish. You can achieve maximum reliability of the connection if you pre-tin the copper wire with solder. If work is carried out using a stranded wire, it must be made single-core by soldering it.
Step 3
Threaded connection is a reliable way of connecting copper and aluminum wires, allowing electrical wiring to be used for a long time. To do this, it is necessary to remove the insulation from the conductors to a length of 4 screw diameters. In the case of oxidized veins, the metal must be brushed to a shine and formed into a circle. In the future, the structure is assembled in this way: a spring washer is put on the screw, then a simple washer, after the circumference of one conductor, again a simple washer, the circumference of another conductor, a washer and finally a nut.
Step 4
4. Subsequently, a screw is screwed into it, and the whole structure is pulled together so that the spring washer is straightened. If conductors with a diameter of less than 2 mm are used, an M4 screw is sufficient. If the end of the copper ring is tinned, there is no need to insert a washer between the two conductors. In the case of a stranded wire, it is recommended to pre-strip it with solder.
Step 5
No less widespread is the method of connecting copper and aluminum wires with a terminal block. For this, it is not necessary to form circles from the conductors, and the connection itself does not need to be insulated, since the structure is designed so as to protect the bare areas from contact with each other. First of all, the end of the wire must be stripped to a height of half a centimeter, inserted into the hole and tightened with a screw. This method is indispensable when connecting the chandelier to insufficient length aluminum wires.
Step 6
To permanently connect the wires, you will need a special tool - a riveter. The conductors are prepared in the same way as for the threaded connection. First place an aluminum ring on the rivet, then a spring washer, then a copper ring and finally a flat washer. After inserting a steel rod into the riveter, you need to squeeze the tool handles so that you hear a click. This method can be used for repair work in the wall if the aluminum conductors have been damaged.