To obtain permanent joints in industry and in everyday life, various types of welding are widely used. In this way, homogeneous metals and their alloys are interconnected. Welding is profitable from an economic point of view, it is characterized by high productivity and ensures good quality of joining materials.
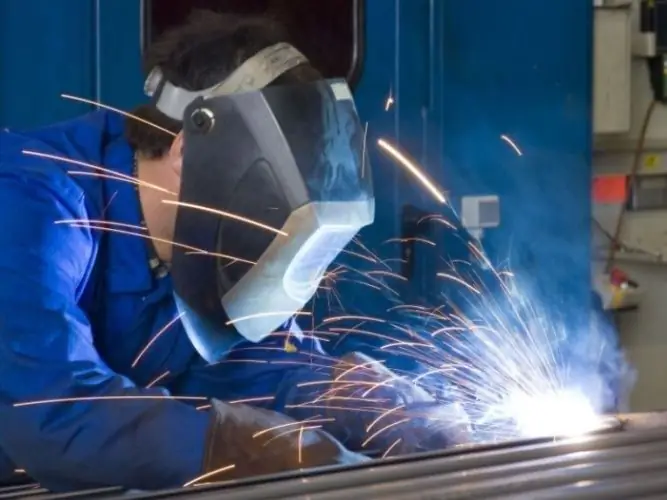
Welding technology
Welding is a technological process in which strong bonds are established between atoms and molecules in the parts to be joined. To ensure such a connection, the surface of the structures to be treated is preliminarily cleaned from contamination, and the oxide film is also removed from the parts. Preparatory work greatly affects the quality of the connection.
The surfaces to be welded are brought together so that the distance between them is minimal. Then the parts are subjected to strong local heating or plastic deformation, after which the blanks are connected, forming a single whole. At the final stage, the weld is processed.
There are three classes of welding: mechanical, thermal and thermomechanical. Mechanical types of welding are carried out using pressure energy, for example, the processing of workpieces by friction, explosion or ultrasound. Thermal welding uses the melting of materials using heat energy. Thermomechanical welding combines the features of the two classes described.
Main types of welding
Arc welding is one of the most common types of such material joining. In this case, welding electrodes are used, which are installed in a special holder and moved along the future seam. An electric arc is formed between the electrode rod and the workpiece, the metal melts and fills the weld, gradually hardening.
In resistance welding, a short heating of the place of joining of parts is performed, which does not imply melting of the edges of the workpieces. In this case, plastic deformation of the metal takes place, which leads to the formation of a welded joint. To heat up the junction during resistance welding, an electric current is used, which is a source of heat. At the points of contact, the metal becomes very ductile, which makes it easier to join the surfaces.
It is widely used in production and gas welding. In this case, the place where the parts need to be connected is strongly heated with a gas flame at a very high temperature. The edges of the workpieces melt under such thermal action. A filler material is fed into the resulting gap, which serves to form the weld. The advantage of gas welding over arc welding is that the workpiece under the action of a gas jet heats up more smoothly. This allows this type of welding to be used for joining workpieces of small thickness.